November / December 2019
A Blacksmithing Primer
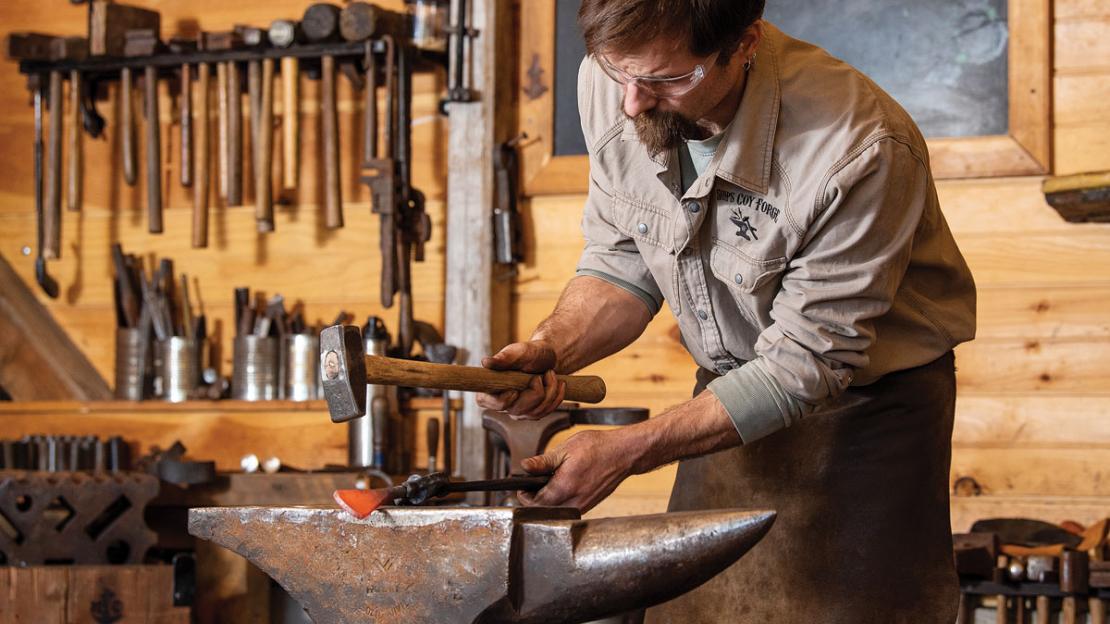
At Ship’s Coy Forge in Lyman, New Hampshire, Med Chandler develops the shape of a caulking iron. These tools are one of the primary products of the forge, which also makes hardware.
Med Chandler makes quality tools by hand. He began learning the blacksmith trade in 2003 at the Fort at No. 4 Open Air Museum in Charlestown, New Hampshire, before stints at Boothbay Harbor Shipyard in Maine and Ball & Ball Reproductions in Pennsylvania. In 2010, Med and his family moved back to New Hampshire and, using reclaimed timbers from a mid-1800s blacksmith shop, built a new forge behind his home. Under the name Ship’s Coy Forge, he has since been producing heirloom-quality tools and replacement hardware.
Caulking irons are a mainstay for Ship’s Coy; the company sends orders for them to locations all around the United States and overseas. Med keeps busy with two lines of iron sizes, “boat” and “ship,” as well as reefing hooks and bottle openers. Last January, he generously allowed me to spend a day in his forge to document his way of making caulking irons from start to finish. The following steps are not intended as a how-to for the backyard blacksmith; rather, they are an overview of the techniques, hard work, skill, and passion required to make these tools.
To read the rest of this article:
Click the button below to log into your Digital Issue Access account.
No digital access? Subscribe or upgrade to a WoodenBoat Digital Subscription and finish reading this article as well as every article we have published for the past 50+ years.
ACCESS TO EXPERIENCE
Subscribe Today
To read articles from previous issues, you can purchase the issue at The WoodenBoat Store link below.