Stitching a Set of Oar Leathers
By Robin Lincoln
By Robin Lincoln
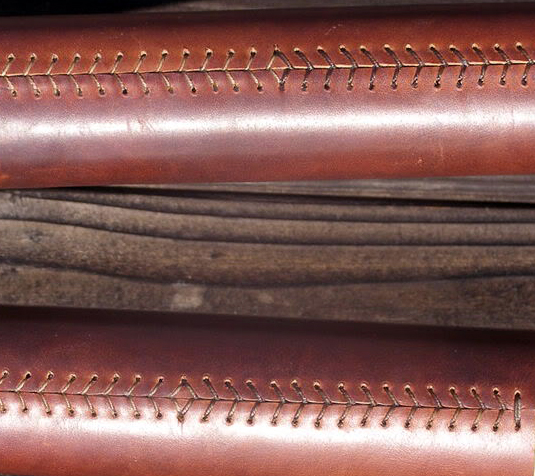
WB No. 230: Stitching a Set of Oar Leathers — This article originally appeared in WB No. 127 (November/December 1995). We present it again here to augment our coverage of dinghies in the Getting Started in Boats supplement bound into WB No. 230. –Eds.
Sewn-on oar leathers are a simple and elegant way to protect fine wooden oars from chafing in their oarlocks. Sewn leather can be easily removed to allow painting or varnishing of the oars or replacement due to wear. Tacked-on leathers, on the other hand, may allow moisture to penetrate the wood, thus making them susceptible to rot along their row of fastenings.
A bit of preparation is required before you begin the process of attaching oar leathers. First, you need to find a suitable piece of leather. Oiled shoulder from a leather shop works well or, alternatively, some marine outfitters sell oar leather kits. You’ll want a thick, pliable, easily bent piece. If it’s too thin or stretchy, it won’t hold its shape and might tear during the sewing.
The width of the piece of leather, of course, depends upon the circumference of the oar’s loom. Generally, a length of 12-24″ is adequate for one leather; use the shorter end of this range if the oars are to be used in only one boat, and the longer one if the oars are to be used in a variety of boats. Also, if you need to protect against over-the-stern sculling, then a longer oar leather should be used. You’ll need a hand-sewing palm, two No. 14 sailmaker’s needles, and some waxed synthetic hand-sewing thread.
1. Take your oars to the boat and lay them, butt ends together, in their rowing positions. Lightly pencil a mark where they touch the oarlocks. Find a workbench or table where you can secure an oar with clamps or a vise, and, after determining the length of leather you’d like to use, center the piece on the mark you made. Draw two new lines to mark the ends of the leather.
2. Lightly sand the shine off the paint or varnish between the two end marks—this roughing up of the surface will help hold the leather in place. Try not to remove the marks.
3. Next comes the most difficult part of the job: sizing and cutting the leather to fit the circumference of the oar. The best way to determine the circumference is to cut a sacrificial strip of leather, 1″ wide and long enough to go around the oar with a little to spare. Usually, oar looms are tapered, so you will need to determine the circumference of the oar at each end of the leather, and at the midpoint. To do this, wrap the sacrificial strip around the loom and pull it snug. Mark with a pen where the two ends of the finished oar leather would touch. Lay the strip out flat, measure the location of your mark from the end, subtract ¼″ from this measurement, and record the result. Do the same for the other two locations, remembering to subtract ¼″.
Now lay the raw leather out flat, rough side up, and with a pen and straightedge draw on it the shape of the finished leather according to your measurements. The shape must be symmetrical lengthwise, and the end near the blade will usually be narrower. Cut the piece out with very sharp scissors, and test its fit on the oar. There should be a ¼″ gap along the seam. If you like the fit, round off the four corners just a wee bit with the scissors. (Be sure to repeat all of this step for the second oar, because the two oars may not have the exact same circumference.
4. Now soak the leather in warm water to soften it. When it is saturated, wring it out. Clamp the oar at the bench so the blade is perpendicular to the floor. The stitching should be positioned so it does not chafe against the oarlock; therefore, the seam should be straight up during the stroke. With a straightedge, mark a pencil line along the shaft indicating the seam location.
5. The sewing procedure requires two needles. String them both up separately with a double length of twine on each, but don’t tie the ends together to form a loop. Instead, melt each end into a small knob that will act as a stopper (a real knot would be too bulky). Each doubled length of twine should be twice as long as the length of leather being sewn. Wrap the wet leather around the oar and line it up with your marks. The seam you are sewing should straddle its pencil line and be parallel to the axis of the loom. The top and bottom of the leather should touch the end marks. You are now ready to begin sewing.
You’ll be using a simple stitch, sometimes called a “baseball stitch.” It is done with two needles to create even tension between the two edges of the leather, as well as for strength. Now get ready, with your palm, to drive a needle into the leather approximately ¼″ from the edge of the seam and approximately ¼″ from the top.
6. Begin sewing on the end closest to the oar grip and work toward the blade. Put the needle through the rough side—the underside— of one edge, and exit on the top surface of the leather. Then stitch straight across the seam, piercing the surface of he leather on the opposite edge and exiting on the rough underside. Repeat the process, so now you have two stitches going straight across the seam and the melted “stopper knob” protected from chafe inside the leather. Take the other needle and repeat these steps, working from the other side. This initial stitching anchors everything together. Make this beginning stitch carefully and slowly. You should now have needles exiting both sides of the seam, and the leather edges should be just butting up to each other. With this step complete, you can begin the actual stitch.
7. Pass one needle over the edge of one side and then, moving it along the loom toward the blade about ½″ to 3/8″, under and through the opposite edge so the needle exits from the top surface of the leather. Do the same with the second needle. Repeat the process: over, under, and through with the first needle, and then over under and through with the second needle, forming a criss-cross pattern.
8. The two threads should cross in the seam, and the leather edges should be just touching as you pull the stitches tight. The row of stitching holes should never be closer to the edge than ¼″, and their distance apart should be a consistent ½″ to 5/8″. You can mark this stitching pattern on the leather ahead of time if you’d like to. You may have to work the leather a bit to keep everything lined up. There should be no tearing at the stitch holes. If there is, then start again with a stronger piece of leather, or close the gap a bit with a new, very slightly wider, piece. As the leather dries it will shrink; this is essential to a tight fit, which is what keeps the leather from sliding up and down the loom.
9. The end stitch is the same as the beginning stitch. Go around twice, and then, after pulling very tightly, cut the threads off 3/16″ from their exit holes and melt them into a knob. Quickly wet your finger and press down on the hot threads to make them flush with the surface of the leather.
10. Using a mallet, gently pound the stitching down so it becomes smooth. Stand back and admire your handwork and prepare to do the other oar. Before you begin, stand the two oars up side by side to mark for the second leather so the two will fall in the same position along the loom. A yearly oiling of the leather with mink oil (or neat’s foot oil for oil-tanned leather) will keep it from drying and cracking and will help maintain its water-resistant qualities.