Hollow Wooden Masts
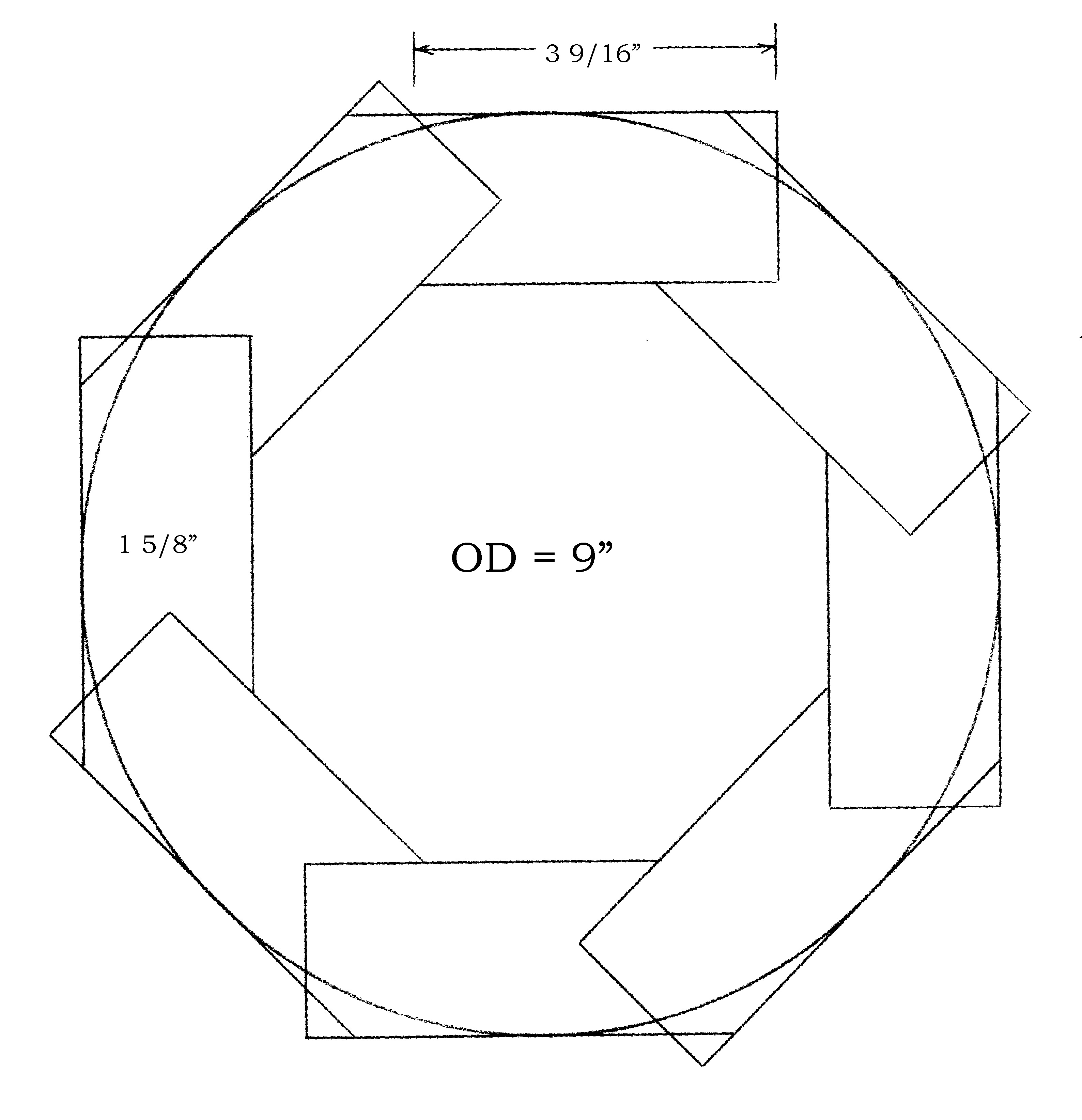
For many millennia, sailboat masts have been made from trees. Trees are an obvious choice, as they are essentially ready-made masts, as if designed and grown for that purpose, which indeed they are, right down to the correct taper. Dry them out, strip the bark off, seal the wood, lash on hardware and rigging and off you go!
Of the tens of thousands of years that this has worked for us, it has only been in the last one hundred and fifty years or so that anything has changed. I think the introduction of the “yacht” had a lot to do with this. As man’s world changed to allow the creation of “leisure” and “sport,” he began to invent boats that could be used for pleasure and recreation instead of fishing and transportation (to say nothing of war).
Lighter, faster, more responsive sailboat hulls correspondingly required taller, lighter, more exotic rigs. Using tall, small-diameter trees for these rigs did not provide satisfactory results: the weight and flexibility of solid masts required too much rigging to support them, and overall weight became an increasing liability. Lighter woods were sought, such as Sitka spruce, but it soon became obvious that what was needed were hollow masts.
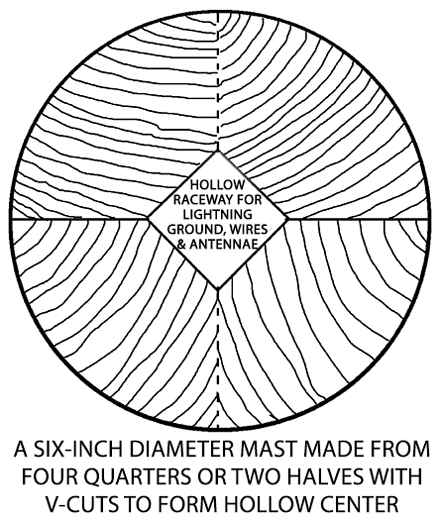
An early method of making hollow masts from large stock.
Early attempts at making hollow masts included burning out the heartwood (not a raging success); drilling out the center (practical only for short lengths); splitting the mast in half, hollowing out each half, and gluing the halves back together (requiring good glue); and making masts from plank stock. The problem came down to finding glue that was both strong and water resistant. Mast halves could be joined using mechanical fasteners (awkward) or binding (vulnerable), and interlocking joinery might be helpful—but ultimately glue was the weak link.
With the invention of “Resorcinol” and “plastic-resin-glues,” new possibilities became available, and with the advent of epoxy, everything changed. The above drawing shows a mast section made from two halves (or four quarters). The V-cut through the center provides a raceway for wires, lightens the mast weight, strengthens it and de-stresses the glue joints by allowing some uneven expansion/contraction. It is preferable to expose “vertical” grain on all exterior surfaces for stability and durability. Because nearly all the strength of a spar is on or near the surface (tension & compression), material beneath the surface adds weight and inertia, thereby weakening the mast. Hence the hollow portion shown may be considerably larger, within reason, depending on whether the mast is stayed or free-standing. The hollow center should decrease in size with mast taper, and be sealed or terminated below the masthead. This method is also excellent for booms and gaffs where some weight is desirable.
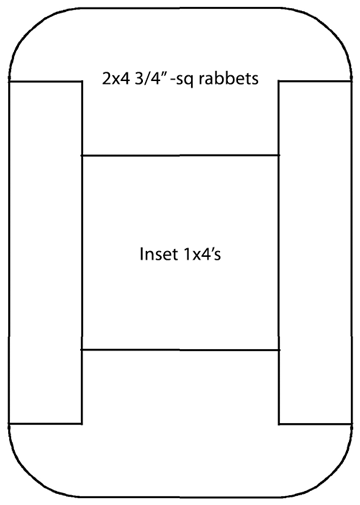
Box section spar, hollow-center, 3 ½″ x 5″
I have used the above method extensively for many years for masts, booms, yards and gaffs with only one failure, which was caused by a poorly placed knot and gale-force winds. My preferred wood for all spars has been Douglas fir, air-dried. For solid spars or two-part laminations (as above), I use #2 material. I often search through lumber yard construction-grade stock, deliberately choosing old, checked, slightly twisted or warped timbers (large material), which I am frequently able to purchase “at cost.” I re-saw and re-surface the timber to straighten it, and to obtain vertical-grain (quarter-sawn) exposed surfaces. There is often substantial waste, which I use for blocking and stack laminations (like deadwood keels).
A very popular lamination technique for sailboat masts and booms employs the “box” section shown to the right. Many yachts employed this method throughout the early and middle years of the 20th century. Such spars were laid up on long “spar benches”, using dozens of clamps to hold pressure on the resin-type glues available at the time. Many of these spars were made from Sitka spruce, and some are still around. With meticulous maintenance, they can be very durable, but they usually failed where metal hardware was attached to them. I sometimes build booms for marconi-rigged boats using this method, as the flat surfaces are convenient for attaching bee-rails, tracks, cleats and cheek blocks. With epoxy glue, very few clamps are required, and I often use a nylon “spiral-wrap” to clamp the spar during curing. By inserting PVC or Nylon tubes (with epoxy) through the wood where hardware is through-bolted, the rot problem is eliminated. You can also use marine plywood in lieu of the solid-wood sides, saving weight and making the box section even stronger and stiffer.
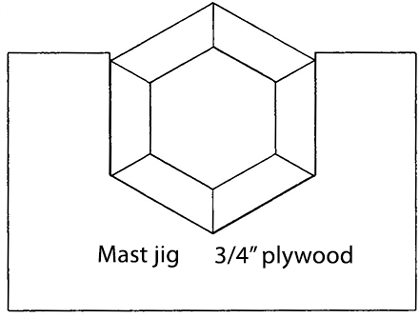
Hexagonal mast section from 2x6 stock; 7 ½″ diameter.
For larger spars in vessels over 35 feet, I borrowed a mast-lamination method from multihull designer Chris White. Chris made a pair of free-standing masts for his big trimaran JUNIPER, leaving them shaped hexagonally with gently rounded corners for sleeved sails. While Chris used splines for his glue joints, I made my spars from thicker segments, eliminated the splines, and rounded the masts instead of leaving them faceted. We made many masts, booms, yards and gaffs with this method, both free-standing and stayed, and had excellent success with them. They are all still in service, some since 1985. The drawback with the hexagonal section is that the mast panels must be fairly thick to achieve good gluing surfaces, adding unnecessary weight. Hence when I was made aware of the “bird’s mouth” method, I switched.
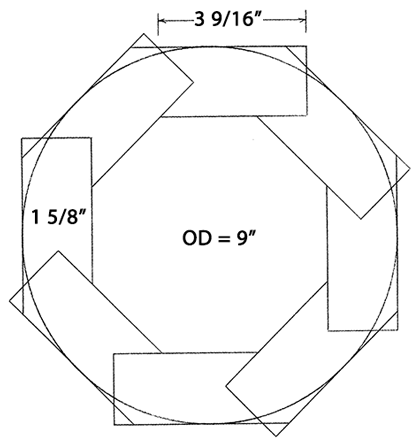
Octagonal/round mast using the bird’s mouth method.
I believe Nathanael Greene Herreshoff may have invented the “bird’s mouth” method of joining eight full-length mast panels together using interlocking joints. By cutting a 45-degree V in one edge of each mast panel, the opposing square edge locks into the V forming an excellent mechanical joint as well as increasing the gluing surface. Note that in all laminated masts, the segments that make up each panel must be long-scarfed (8:1) together prior to mast lay-up, and that the scarfs should be staggered between adjacent panels by at least 24.″
When possible, I use air-dried, clear, heart, vertical-grain Douglas fir plank stock in my hollow laminated masts. I have, at times used kiln-dried Douglas fir, but panel-thickness is limited to 1 ½,″ and the cells are damaged by the intense heat. A friend made a mast from kiln-dried Engelmann spruce, which is still in service after 25 years. The key is to saturate the wood, inside and out, with penetrating epoxy. It is best to epoxy prime and polyurethane paint the mast exterior for low maintenance and longevity.
In a future blog, I will describe making masts using the bird’s mouth method. I will also describe making rotating wing masts.
Appleton, Maine, 11/18/2013